Quality Assurance
MGC, under our own quality policy, promotes Company-wide quality assurance activities (Q-MGC) with an overview of the supply chain in order to provide superior products and services with high safety and reliability.
The MGC Group Basic Policy on Quality
- Drive innovation to provide high-quality products and services that meet society's needs in order to gain consumer satisfaction and trust and help customers resolve their problems and achieve sustainable growth.
- Recognize that product and service quality assurance is an important management issue, ensuring the availability of resources (people, infrastructure, environment for the operation of processes) needed to maintain, assure, and improve quality. We will also enhance quality education, working to improve employee awareness of quality-related issues and enabling them to acquire the necessary knowledge.
- Ensure that all departments closely involved in quality—not only quality assurance and quality control departments but R&D, manufacturing, procurement, distribution, sales, and others—have a strong awareness regarding the need to maintain, assure, and improve quality and that each fulfills its responsibilities, striving toward continuous improvement in quality assurance activities.
Quality Assurance Activities
MGC promotes Company-wide quality assurance activities (Q-MGC). Along with providing superior products and services with high safety and reliability, all divisions act in accordance with the MGC Group Basic Policy on Quality in order to thoroughly ensure quality control and assurance.
The Quality Assurance Meeting, which is chaired by the President, is composed of directors, auditors, and workplace managers. Basic matters, such as the Q-MGC annual plan, are discussed and decided, and reports on implementation status are received. In addition, we have established the Quality Assurance Supervisors Meeting, composed of the people in charge of quality from each organization, where we discuss and consider the Q-MGC implementation plan, audit plan, and education/support plan.
All plants have acquired ISO 9001 certification, the international standard for quality management systems. In addition, we have products with FSSC 22000 certification for food safety management systems and ISO 13485 certification for medical devices quality management systems.
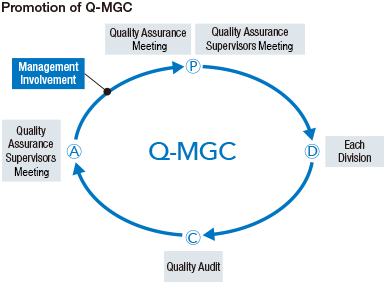
Quality Audit
For quality audits, the quality assurance director and the audit team evaluate the Q-MGC implementation status of all divisions.
Quality audits are conducted in accordance with priority audit items, such as the status of change control, the quality assurance and control of contract manufactured products, goods purchased and sold, and the corrective actions for quality complaints and problems. They are established every year.
In addition to correcting issues, it is also used as a place to extract and share good points.