Occupational safety and health / Process safety and disaster prevention
- Policies on Occupational Health and Safety, Process Safety and Disaster Prevention
- Setup to Promote the Occupational Health and Safety, the Process Safety and Disaster Prevention
- Occupational Health and Safety
- Process Safety and Accident Prevention
- Certified high pressure gas plants
- Safety Performance
- Collection and Dissemination of Safety Information
Policies on Occupational Health and Safety, Process Safety and Disaster Prevention
We undertake safety measures in accordance with the Safety Philosophy and Safety Principle and with "participation by all" as our motto and a goal of achieving zero occupational injuries by employees and the employees of cooperating companies who work at MGC.
Each business site implements voluntary safety measures under its own initiatives, and LINK, a Company-wide organization, conducts Company-wide improvement measures.
In addition, reducing equipment breakdowns and production suspensions is also effective for preventing accidents, and accordingly, we conduct systematic maintenance of facilities and are reinforcing measures at production sites centered on TPM activities*.
- * Total Productive Maintenance activities: Activities that continually realize productivity improvements and the securing of revenue by eliminating all possible losses existing within the production system
Safety Philosophy
Ensuring safety is the top priority of our business activity
Safety Principle
(1) Fostering a Safety Culture
(2) Confirming and Abiding by Safety Rules
(3) Thorough Education and Training
(4) Comprehensive Preventive Maintenance
Safety Slogan
Build a safety culture together through keen awareness and certain knowledge.
Setup to Promote the Occupational Health and Safety and the Process Safety and Disaster Prevention
MGC holds the Environment and Safety Manager Meeting, a gathering of the heads of environmental and safety departments of each workplace to report on and discuss the status of RC measures, and meetings of the LINK Leaders Conference, which discusses LINK activities at each workplace, multiple times each year.
At environment and safety meetings, which are chaired by the President and are held once a year, activities are reviewed, plans for the following year are discussed, and the PDCA cycle is implemented to continuously enhance the levels of activities.
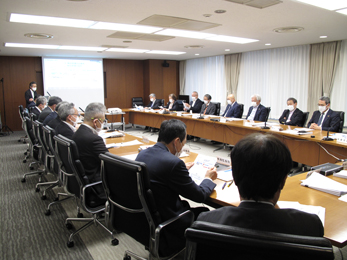
Occupational Health and Safety
With the goal of achieving zero occupational injuries, we regularly conduct safety-related education and drills and occupational health and safety risk assessments. In addition, each workplace continuously engages in everyday safety tasks such as 5S activities, hazard prediction, and proposals for addressing Hiyari Hatto (near-miss) incidents.
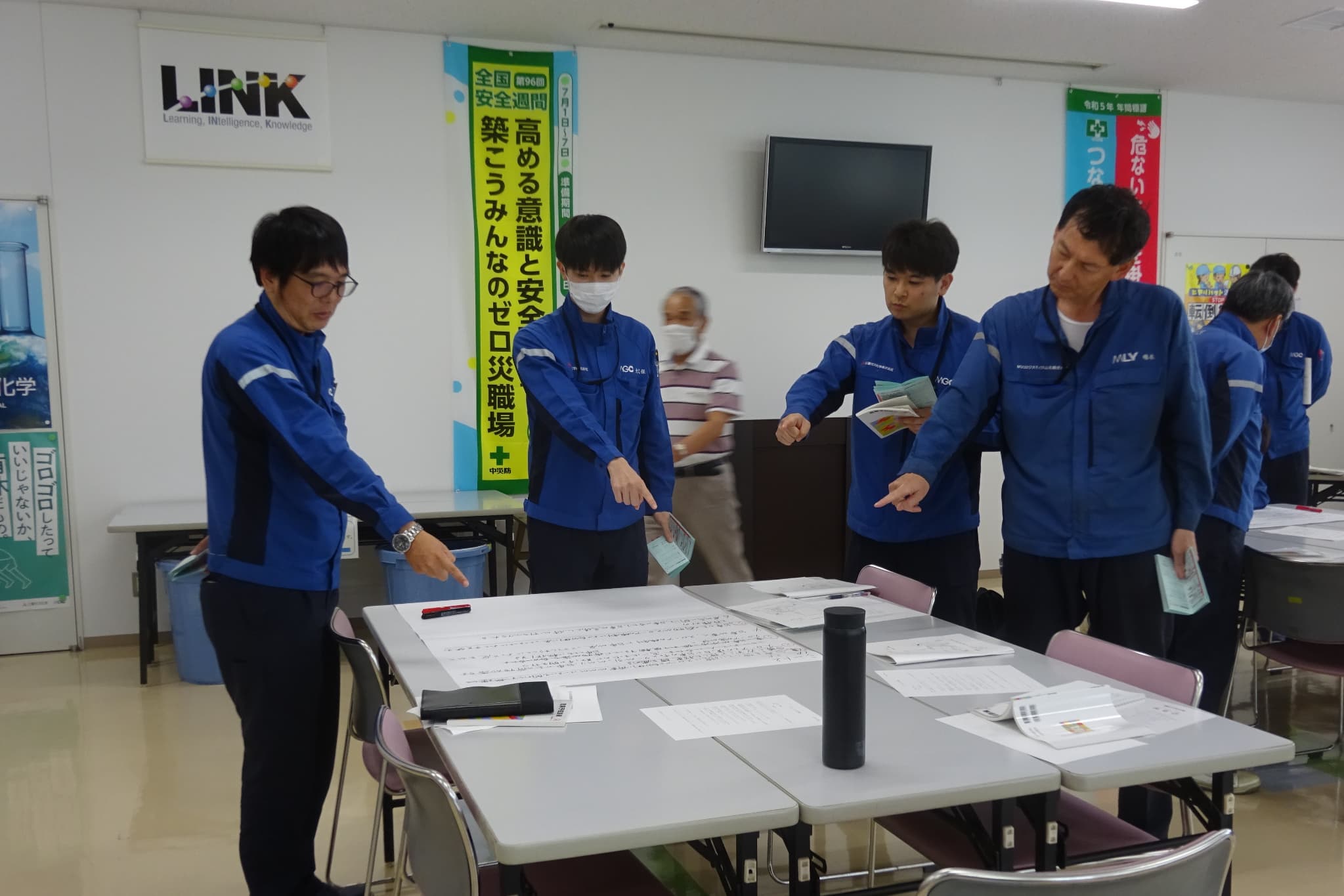
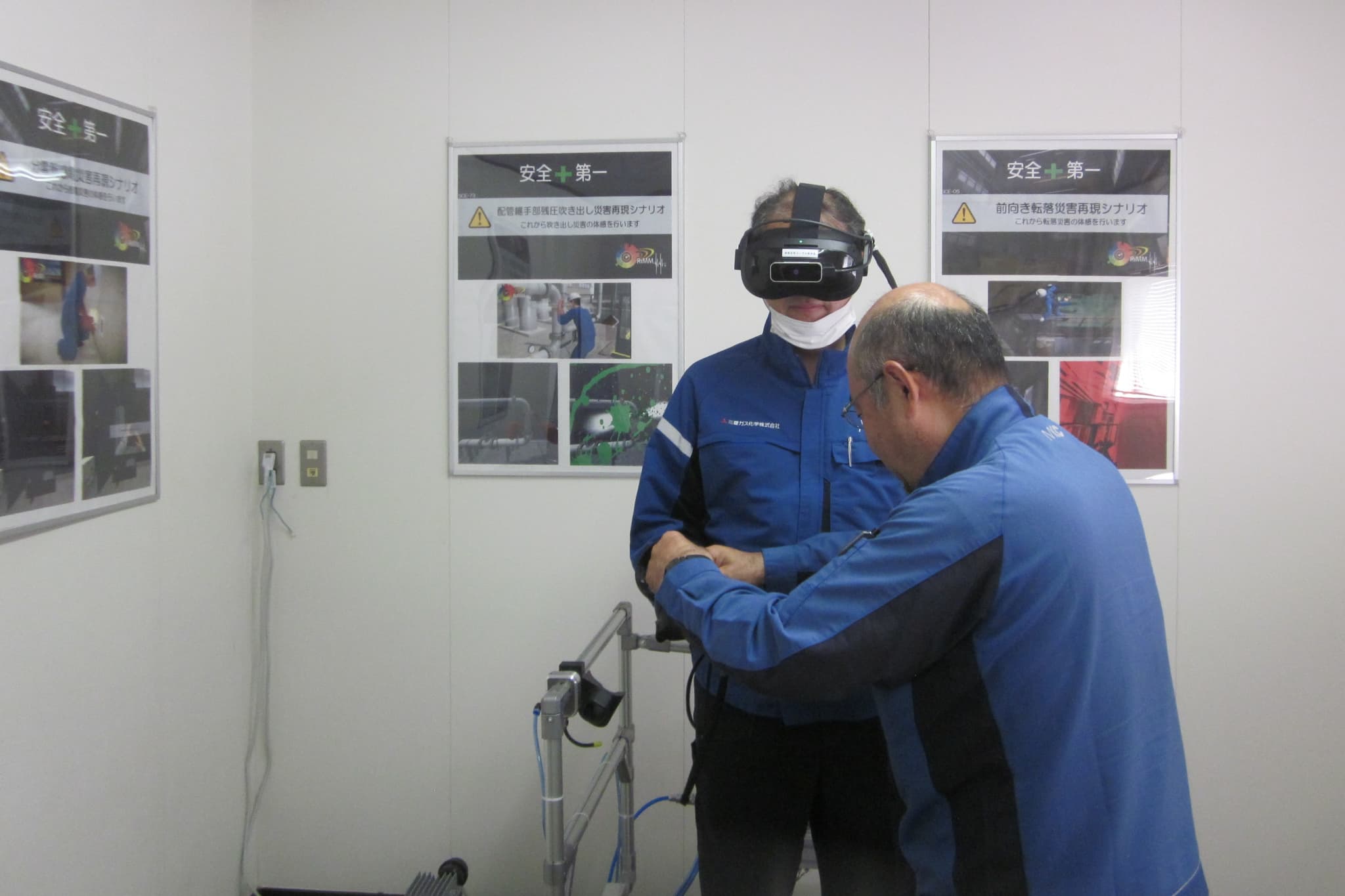
We share information on occupational injuries, perform risk assessments, provide safety education, and carry out joint disaster mitigation training to prevent industrial accidents at partner companies, while working to enhance our cooperative frameworks.
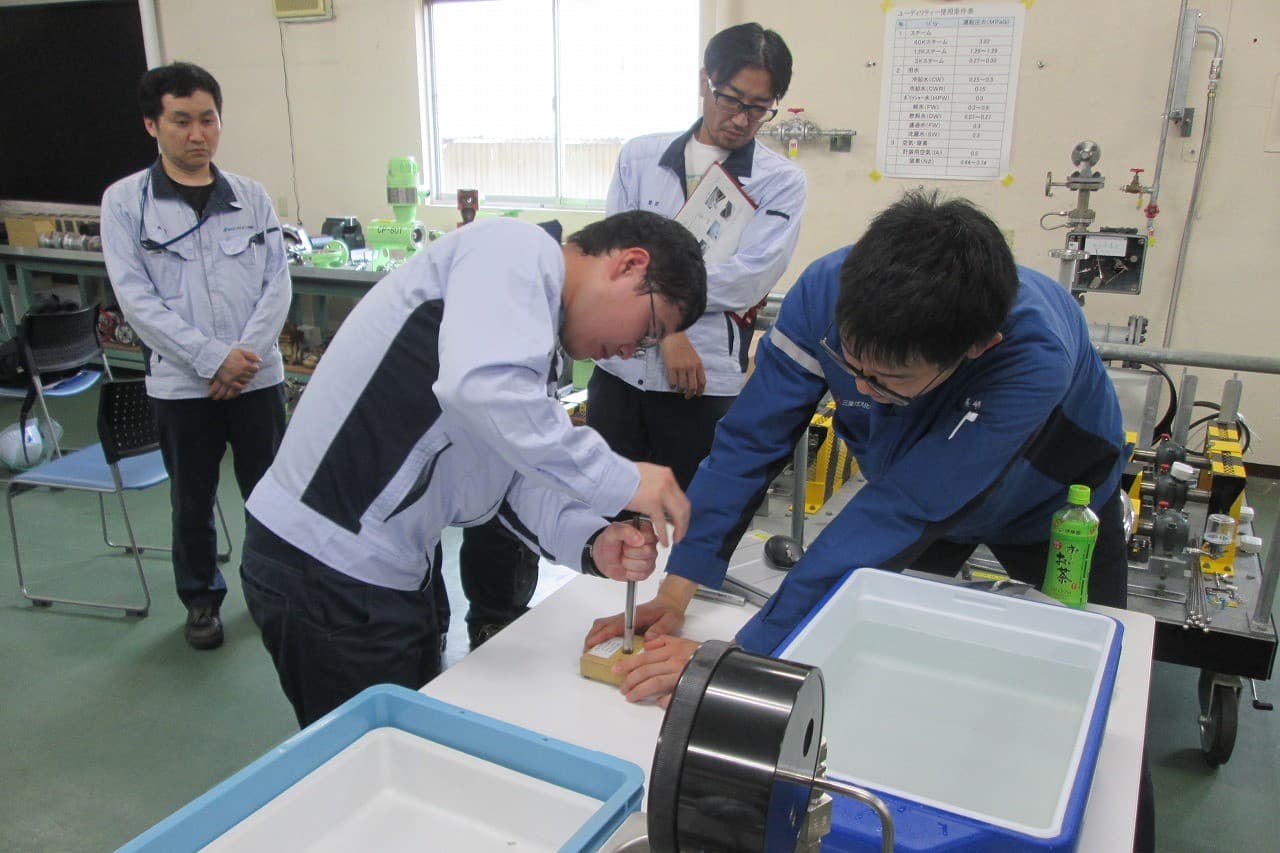
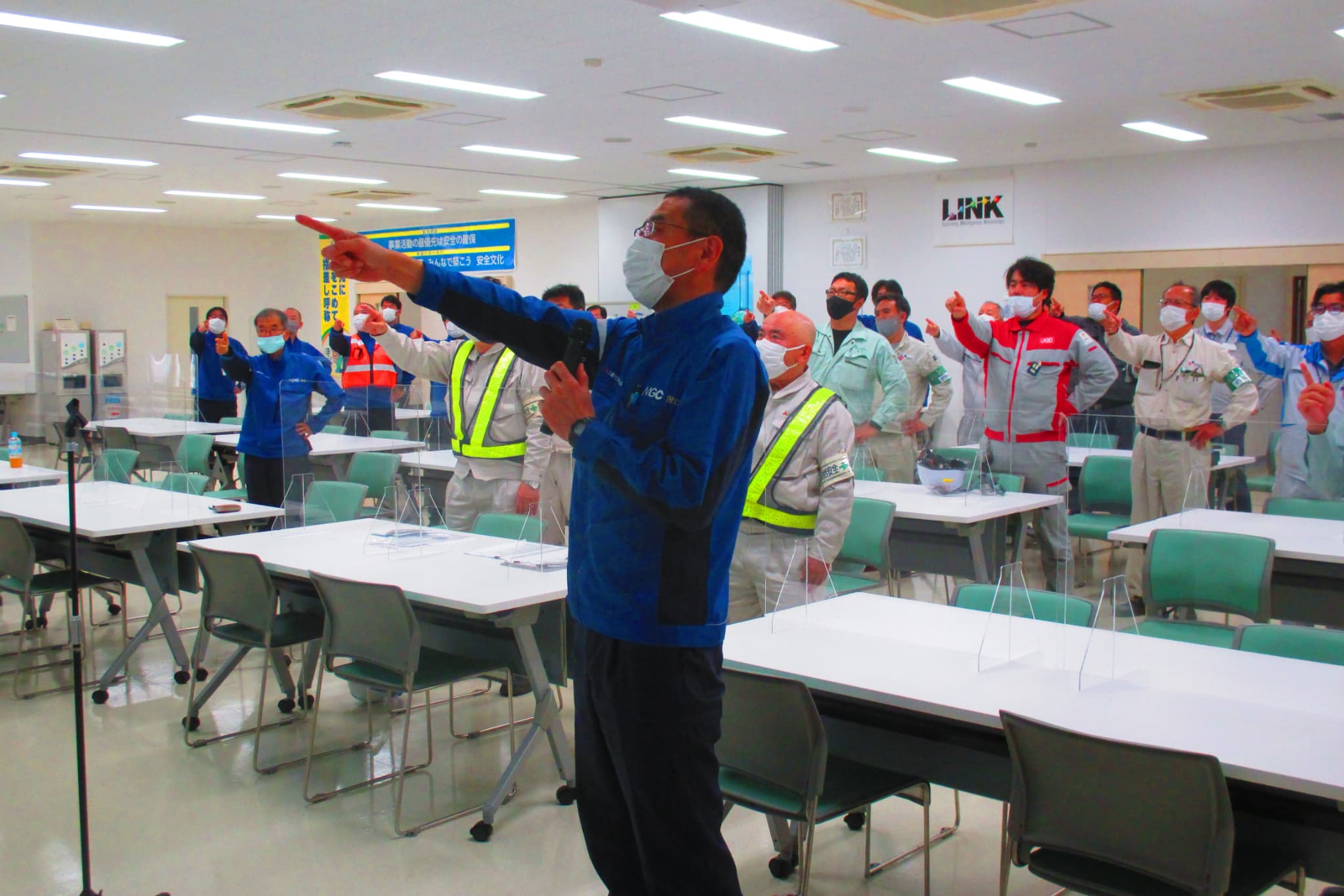
Process Safety and Accident Prevention
To prevent the occurrence of accidents and injuries, it is important to continue stable operations by ensuring the safety of production processes and the soundness of equipment. At each plant, we utilize equipment maintenance system and other systems to conduct checks and make renewal plans, and perform checks, repairs, and renewals with priority set according to risk and the importance of facilities.
We are also using case studies of past accidents to verify the effectiveness of countermeasures and engaging in initiatives aimed at preventing the occurrence of similar accidents. We carry out facility risk assessments that simulate non-steady-state operations, such as emergency shutdowns.
Furthermore, in addition to converting standards manuals to "Know Why," we are also introducing operation simulation training.
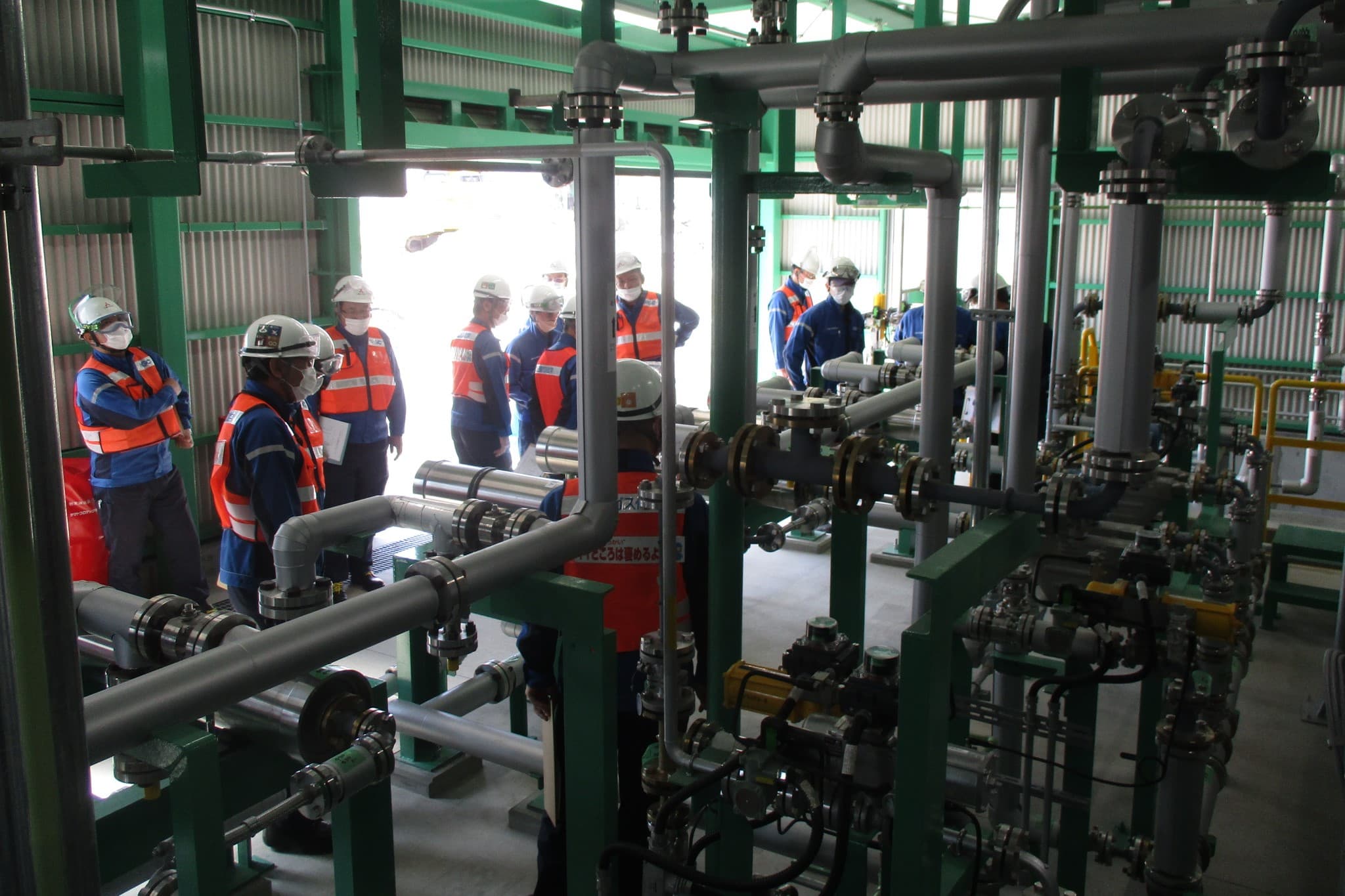
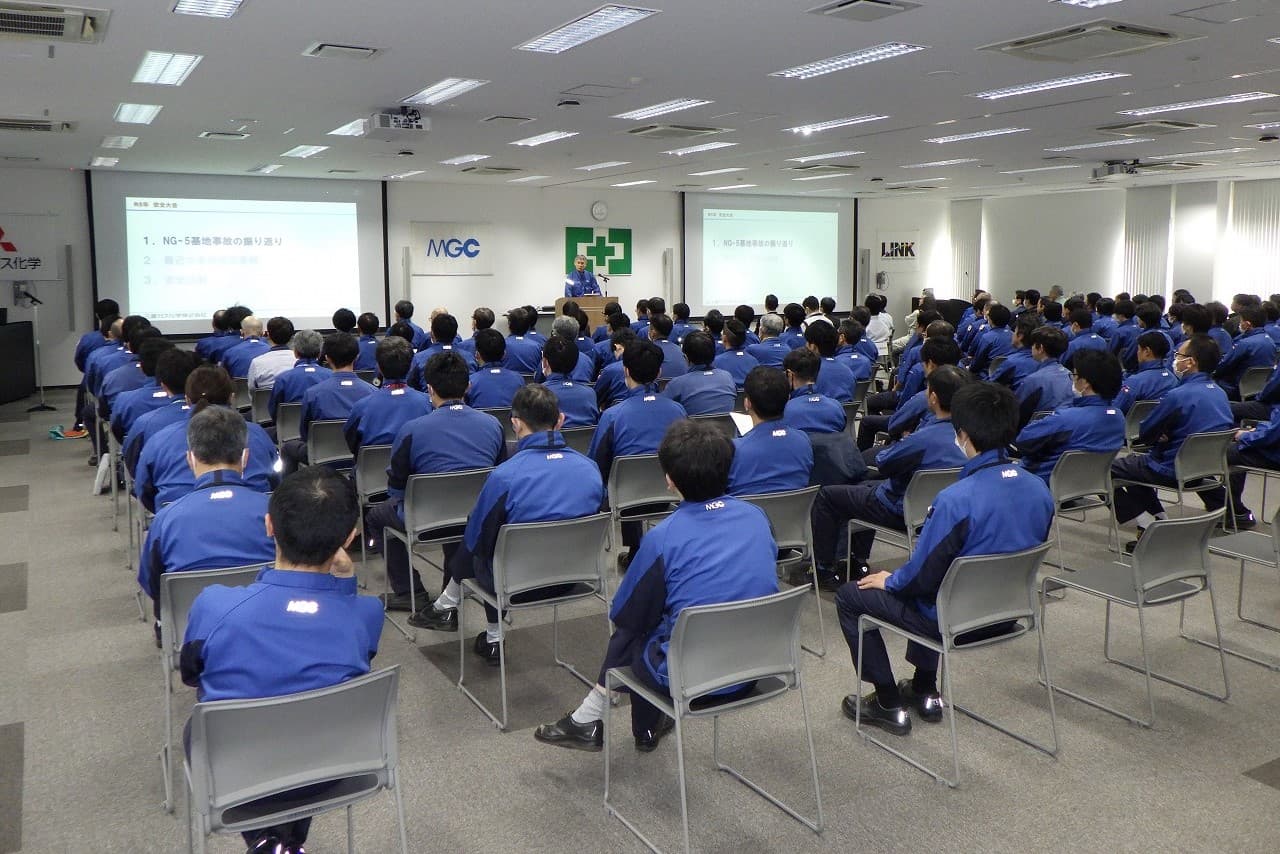
Responding to emergencies
In preparation for accidents, we establish a self-disaster readiness framework at each business site and carry out various disaster reduction drills according to sites' annual plans.
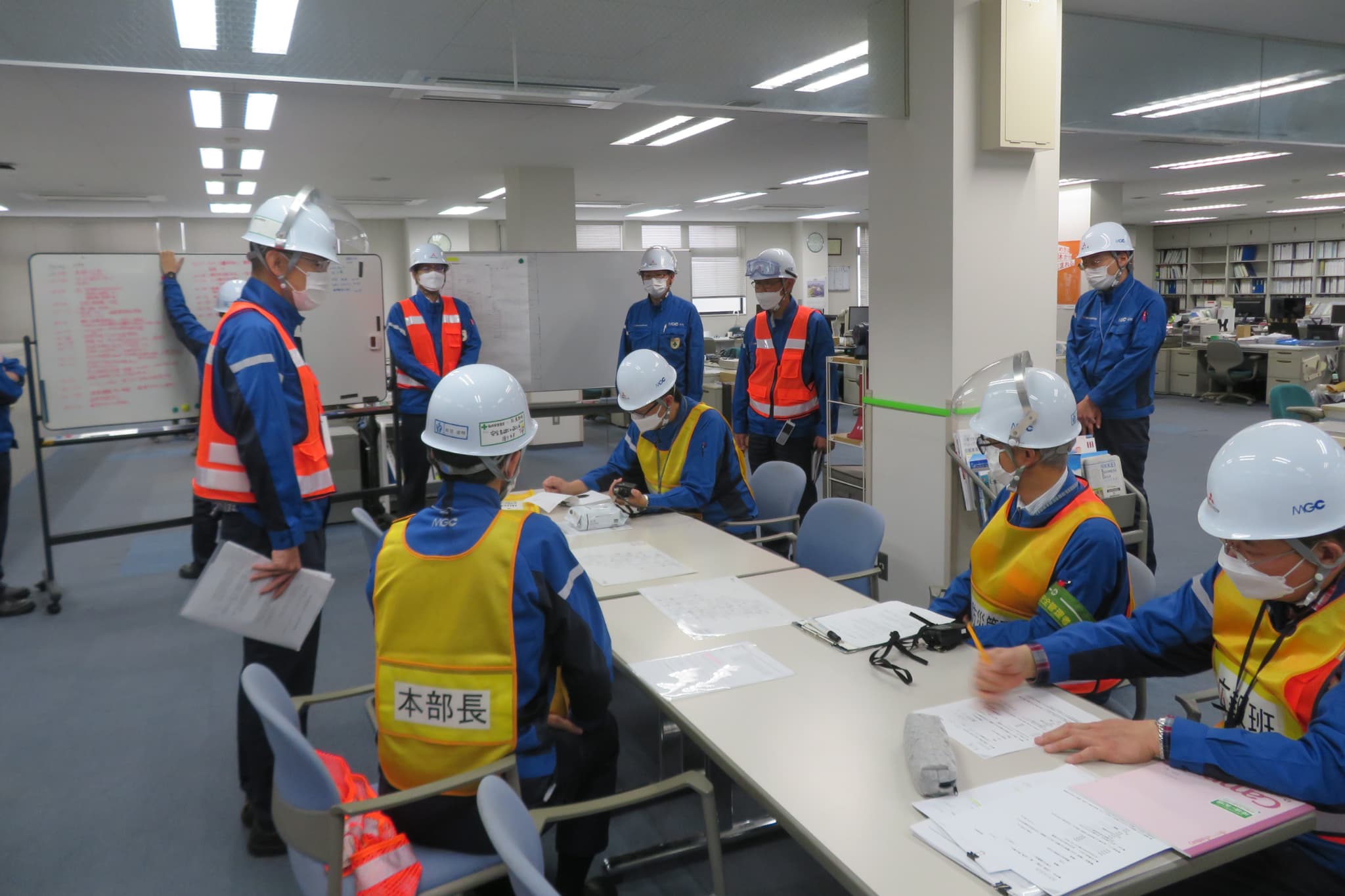
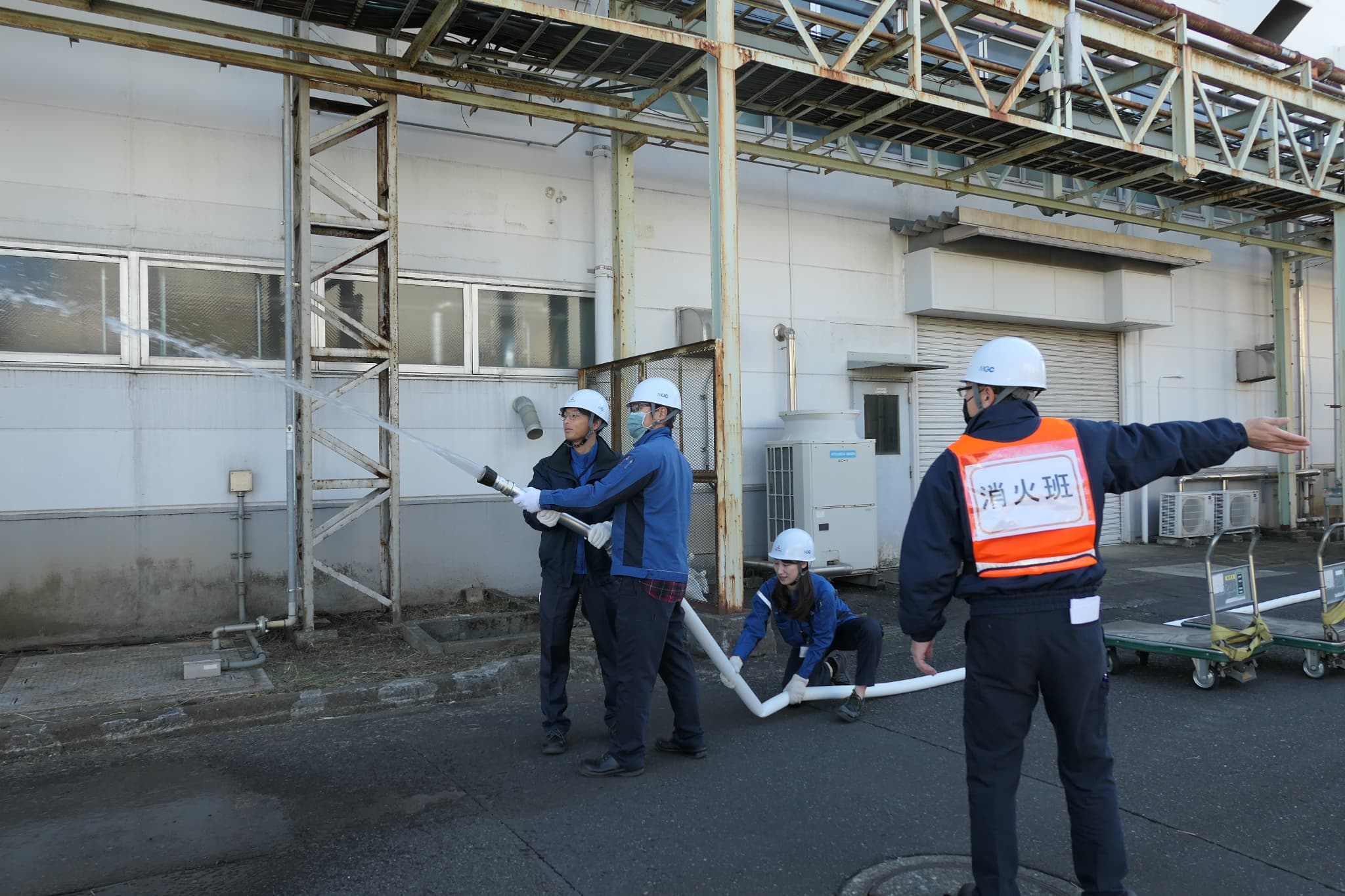
Certified high pressure gas plants
The Niigata Plant and Mizushima Plant, which are high pressure gas safety management code certified plants, are audited by the Director in charge of Environment Safety & Quality Assurance Division (Process Safety Management General Controller) under the company rules for "High pressure gas certification safety management". The aim of our audits is to objectively evaluate the high pressure gas safety management system and the certified inspection management framework to ensure that they are working effectively.
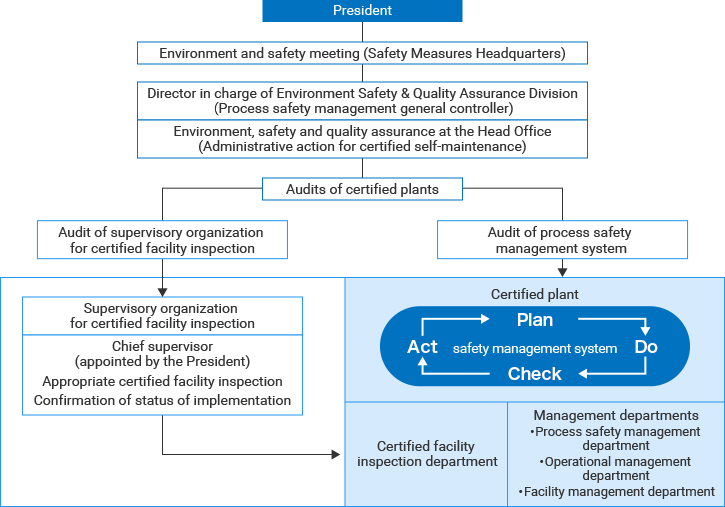
Collection and Dissemination of Safety Information
When accidents or incidents occur at this company, partner companies, or Group companies, MGC immediately relays the information using our safety information transmission system in an effort to prevent the reoccurrence of similar accidents or incidents.
Our plants hold accident prevention meetings and other activities with partner companies to share information.
We share information with Group companies that handle or manufacture chemical substances and promote environmental and safety activities.
Domestic Group Companies that Participate in Information Sharing (15 companies)
EIWA CHEMICAL IND. CO.,LTD.
FUDOW COMPANY LTD.
JSP CORPORATION
MITSUBISHI GAS CHEMICAL NEXT COMPANY, INC.
MGC Advance Co.,Ltd.
MGC AGELESS Co., Ltd.
MGC Electrotechno Co., Ltd.
MGC Farmix Co., Ltd.
MGC Filsheet Co., Ltd.
MGC Terminal Company, Inc.
MGC Woodchem Corporation
SHINSANSO KAGAKU CO.
TOHO EARTHTECH,INC.
Toyo Kagaku Co., Ltd.
Yonezawa Dia Electronics Co., Inc.
Overseas Group Companies that Participate in Information Sharing (12 companies)
AGELESS (THAILAND) CO.,LTD.
MGC ADVANCED POLYMERS, INC.
MGC ELECTROTECHNO (THAILAND)CO.,LTD
MGC PURE CHEMICALS AMERICA, INC.
MGC PURE CHEMICALS SINGAPORE PTE. LTD.
MGC PURE CHEMICALS TAIWAN, INC.
MGC SPECIALTY CHEMICALS NETHERLANDS B.V.
MITSUBISHI GAS CHEMICAL ENGINEERING-PLASTICS(SHANGHAI)CO., LTD.
P.T. PEROKSIDA INDONESIA PRATAMA
SAMYOUNG PURE CHEMICALS CO., LTD.
THAI POLYACETAL CO., LTD.
THAI POLYCARBONATE CO., LTD.