Chemical Substance Management
As a responsible provider of chemical products, MGC clearly explains properties, safety, and handling of its chemical products and conducts various activities to protect the environment and ensure the health and safety of all who use our products.
Safety Policy for Chemicals and Other Products
The policy of MGC is to ensure safety in the handling, use, and disposal of chemical products in accordance with our Safety Philosophy and Safety Principle.
Setup to Promote the Safety of Chemicals and Other Products
All MGC divisions promote Responsible Care in line with the MGC Group Basic Policy on Environment and Safety. We formulate RC Medium-term Plan and annual plan, report the state of progress of these plans to the environment and safety meeting, which meets once a year and is chaired by the president, and obtain approval. Continuous improvements are made by rotating the PDCA cycle in this way.
Safety Activities for Chemicals and Other Products
At MGC, we conduct basic surveys and safety assessments at the product development stage. When products correspond to new chemical substances, we first conduct safety testing and then classify the products according to whether they do or do not come under applicable regulations, as well as according to their degree of hazard under such standards as GHS,* before preparing safety data sheets (SDSs) and other safety information. Based on these, we perform risk assessments (based on hazards of the substances themselves and hazards related to exposure) for every stage of a product, from manufacture to disposal. Products are offered once this screening (premarketing investigations) is complete.
Many of MGC's products are chemicals, and potential product-related accidents include fires and chemical burns. We present hazard information about chemicals with SDSs, product labels, and yellow cards given to customers and others concerned to ensure that products are handled safely. Regarding products destined for overseas markets as well, we supply hazard information through translated SDSs and other means.
* GHS: The Globally Harmonized System of Classification and Labelling of Chemicals. Chemical hazards are classified under fixed standards and are indicated clearly with pictograms on labels and through SDS documentation. Ultimately, the information contributes to accident prevention and to protecting human health and the environment.
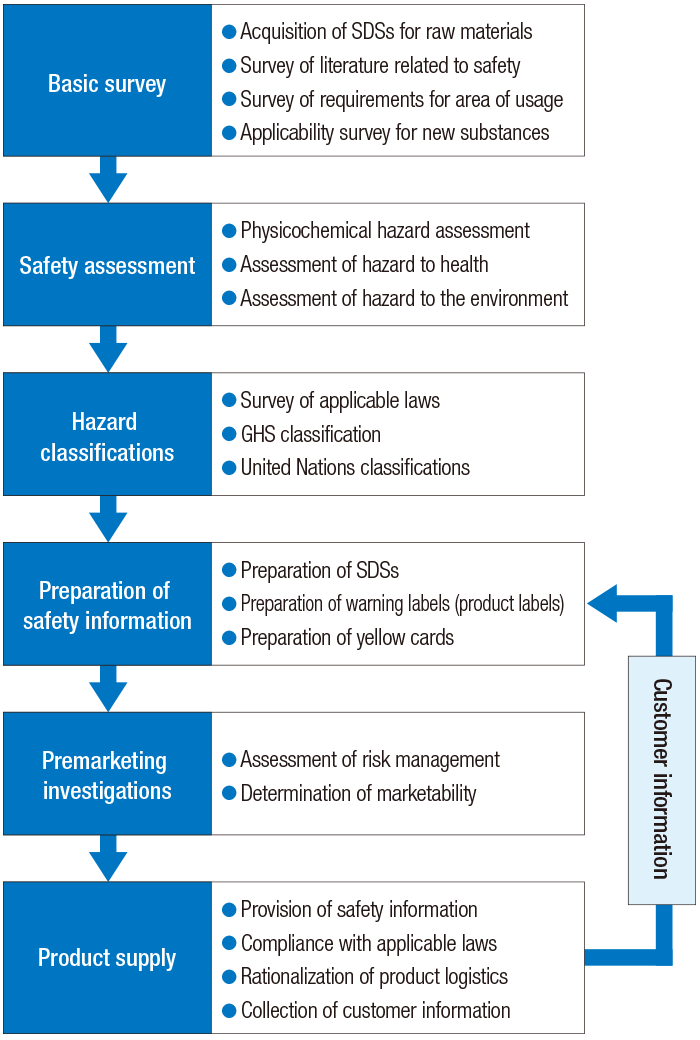
Providing Safety Information
MGC provides safety information on chemicals through means including submission of product SDSs, placement of product warning labels on containers, and distribution of Yellow Cards.
Safety Data Sheets (SDSs)
SDSs are documents that convey detailed information about the handling and safety of chemicals and are submitted to companies that handle MGC's chemicals, such as customers, sales agents, and shipping companies. MGC prepared SDSs that conform to GHS-compliant JIS (JIS Z 7253).
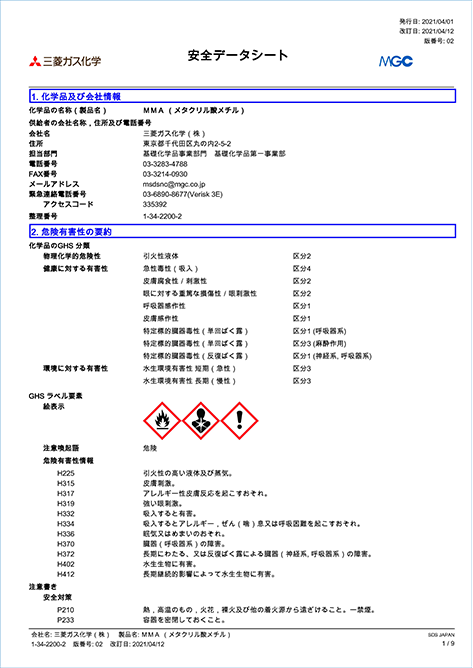
Labels
Easy-to-understand GHS-compliant warnings and safety information for users are printed on labels affixed to our chemical products.We are revising SDSs by reviewing the safety information and are revising labels as well.
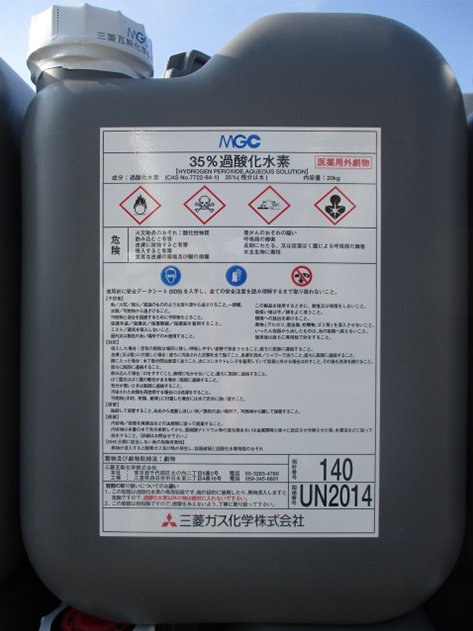
Yellow Cards
A Yellow Card is a card readied in preparation for an accident during domestic shipment. It briefly lists a product's properties, laws that apply to the product, and emergency response measures, as well as contact information including fire departments, police departments, and MGC. We distribute these cards to shippers of chemicals and ensure that they are carried during product shipments.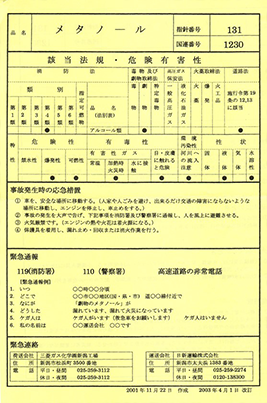
Chemical and Product Safety Education
MGC conducts education on chemicals management and product safety at each business site.
Each year, we take up appropriate topics, such as contents of laws and regulations*, product liability incident case studies, and methods of assessing and classifying hazards and toxicity of the chemicals based on GHS. At sites where chemicals are handled, we provide education on those substances and perform risk assessments at substances designated by the Industrial Safety and Health Act.
*Act on the Regulation of Manufacture and Evaluation of Chemical Substances, Industrial Safety and Health Act , Product Liability Law
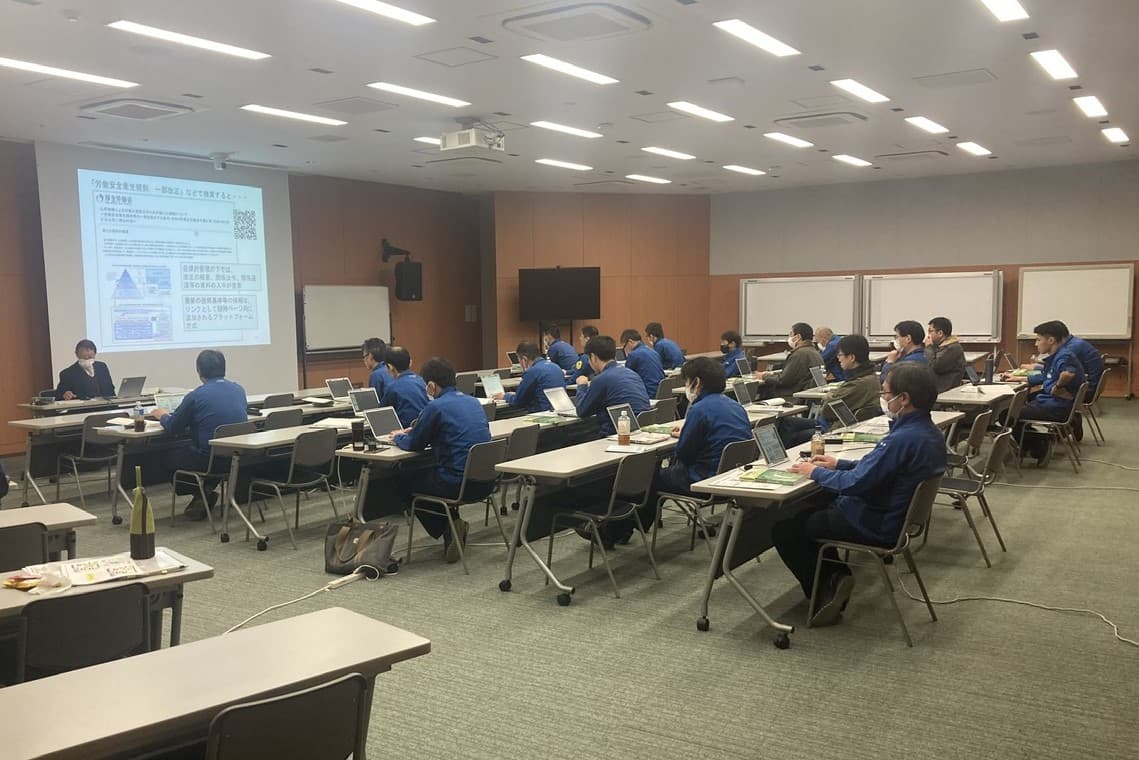
Ensuring Safety during Transportation
MGC educates transportation companies on chemical substance safe handling methods and conducts audits to confirm that transportation companies are handling chemical products properly. We also periodically exchange information with transportation companies and work to ensure safety during transportation.
Responses to Accidents during Transportation
MGC readies emergency materials (sandbags, oil barriers, absorption mats, neutralizing agents, and so on) in preparation for leaks of chemical substances caused by accidents during transportation. We also conduct drills with transportation companies to enhance our ability to respond to emergencies.
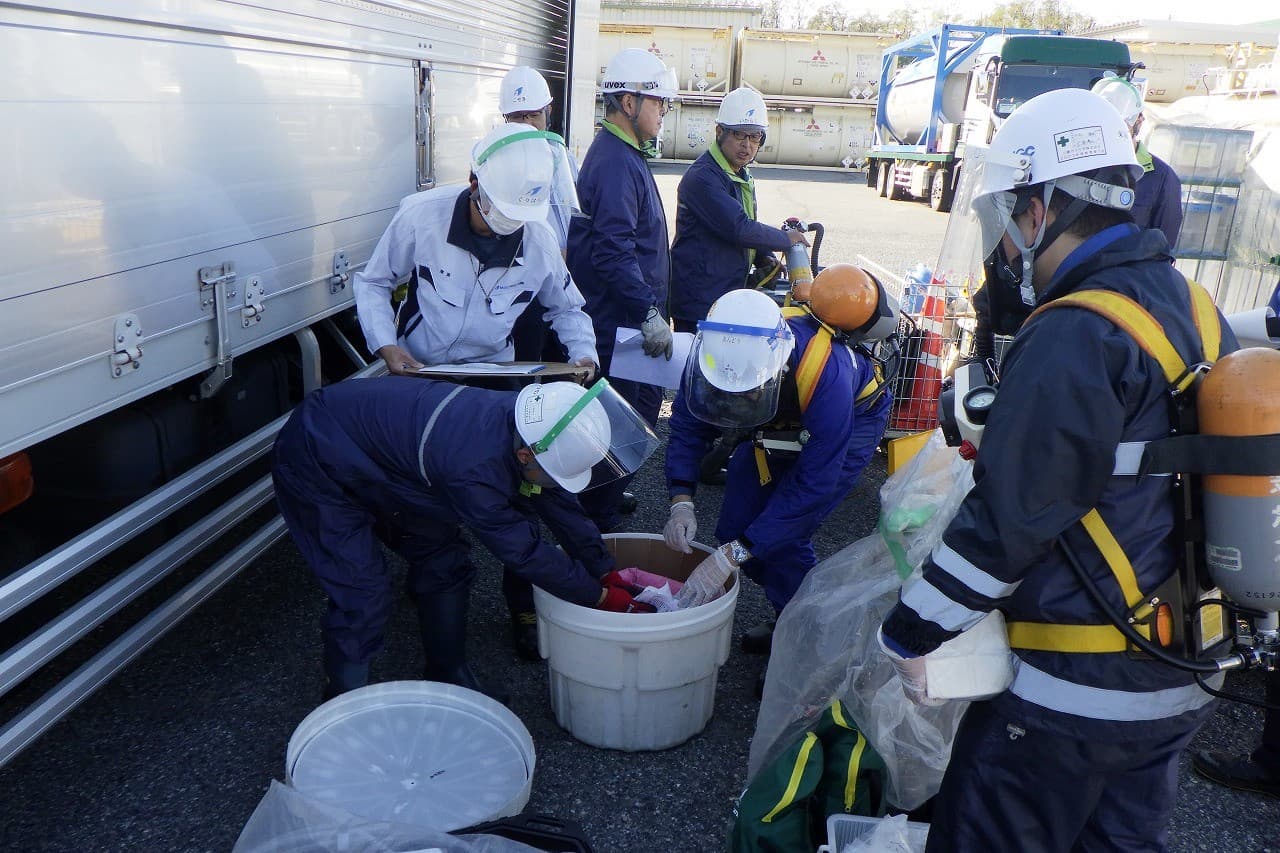
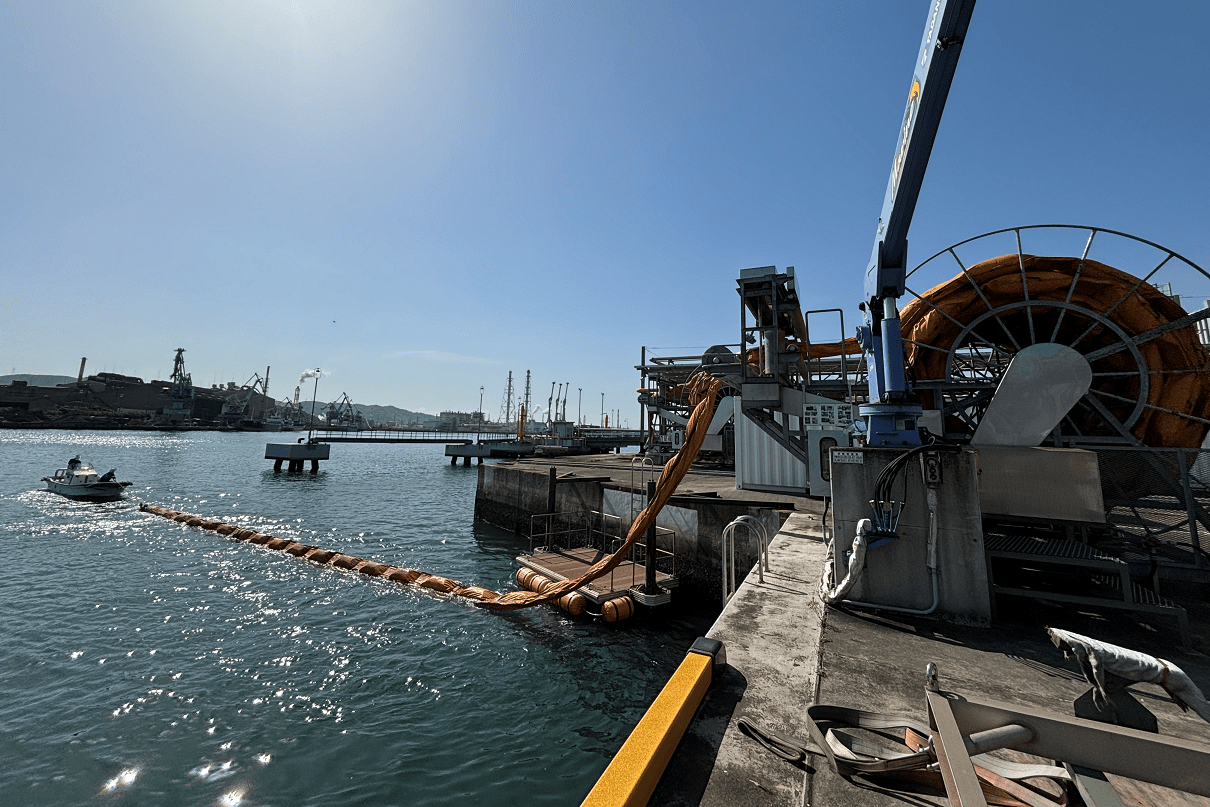