半導体パッケージの歴史を変えた
BT積層板
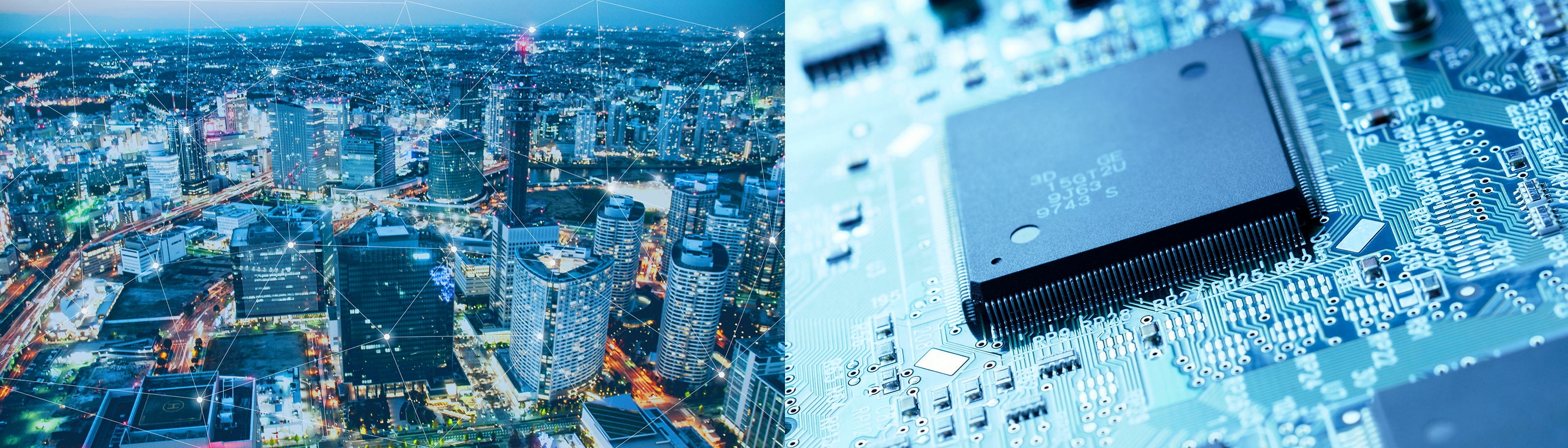
世界シェア
No.1
セラミックを越えた“樹脂製”半導体基板
電子機器の進化はこれ抜きには語れない
「半導体パッケージの歴史を変えた」と言われる「BT積層板」。日本で初めてプリント配線板※1用のプラスチック材料を開発したメーカーである三菱ガス化学(MGC)の自信作です。「BT樹脂※2」の採用で高性能化と低コスト化の両方を実現し、材料革命を起こしたこの基板は、今なお進化を続け、電子機器と情報技術の発展を支え続けています。
- ※1 プリント配線板:ベースとなる積層板※3の上に配線をプリントしたもの。
- ※2 BT樹脂:ビスマレイミド・トリアジン樹脂の略称。BTレジンとも。三菱ガス化学が開発した熱硬化性樹脂で、高い耐熱性とすぐれた電気特性が特徴。
- ※3 積層板:ガラス繊維布などの基材に熱硬化性樹脂を含浸・乾燥させたシートを複数枚重ねて、プレス加工したもの。
01安価、高耐熱、すぐれた電気特性――高性能半導体=セラミック基板の“常識”を覆したBT樹脂
モントリオールオリンピックが開催された1976年、三菱ガス化学は、その後の半導体パッケージの歴史を変えることになる画期的な樹脂「BT樹脂(BTレジン)」を開発しました。当時、高性能半導体を搭載する積層板(プリント配線板)材料といえば高価なセラミックが主流でしたが、BT樹脂はセラミックに比肩する耐熱性と電気特性を実現。このことが高く評価され、1985年に樹脂材料として初めて半導体パッケージ用の積層板に採用されることになったのです。こうして誕生した半導体パッケージ用の「BT積層板」は、セラミック基板と同等の性能を実現でき、価格は安く、加工もしやすいことから、1990年代に急速に国内外の市場に浸透し、多くのパッケージで基板として採用されることになりました。約40年を経た現在も、半導体パッケージ用の積層板材料として世界中で使用されています。
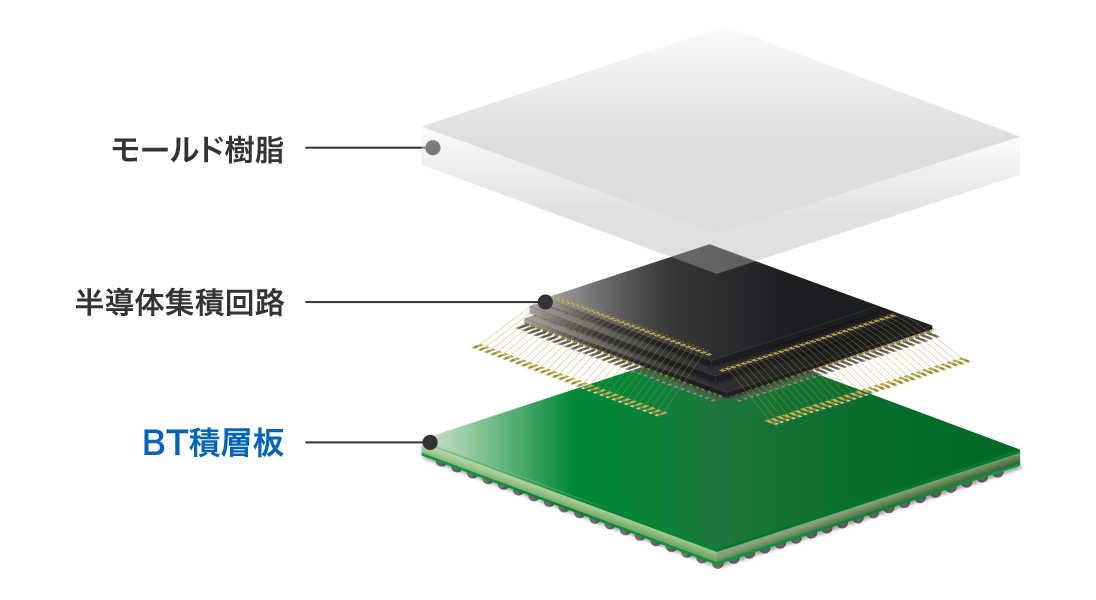
02“スマホ”の進化も半導体から。BT積層板が進化し続ける理由
パソコン、家電製品、自動車、ロボットをはじめ、電気で動くものにはほぼすべて半導体が搭載されています。これらの機器は日々、より高機能・高性能になり、機器によっては小さく、軽くなっています。スマホことスマートフォンはその典型。新しいモデルが登場するたびにできることが増えています。
こうした要求に応えて、電子機器に内蔵される半導体もまた進化を続けてきました。「小型化」と「高機能化」を両立するために、半導体パッケージの中ではどんどん部品の密度が高くなり、当初は100ミクロン以上あったプリント基板の配線間隔もいまや20ミクロン以下となっています。そんな状況下にあるプリント基板にとって、一番の大敵は「温度変化」。BT材料はもともと温度変化による変形が少ない「低反り材※」ですが、油断は禁物です。ON-OFFのたびに膨張や収縮を繰り返しても半導体への影響を最小限にできるよう、日々、改良が続けられています。膨張・収縮の幅をこれまで以上に小さくする、それによる劣化を防ぐといったアプローチがその一例です。デバイスが進化するとき、常にBT積層板も進化しているのです。
- ※低反り材:温度変化があっても反り返りにくい材料のこと。プリント配線板は製造工程でも加熱・冷却が繰り返されるため、温度変化があっても変形しにくい材料が不可欠となる。
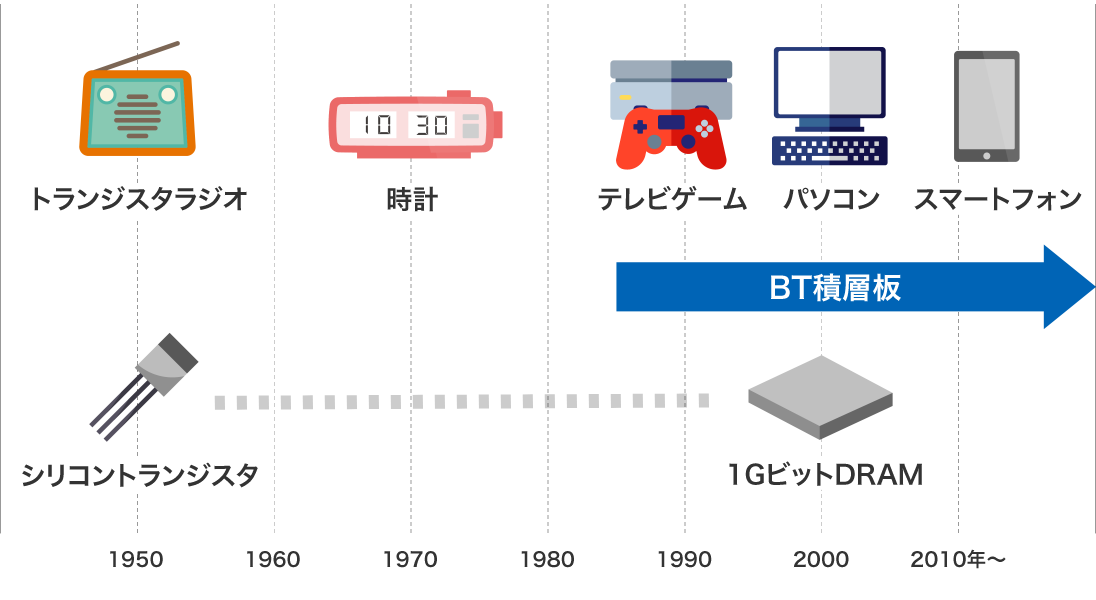
03AIで、IoTで。
情報技術の未来を担う半導体のため、
さらなる高次元の基板材料を目指す
今なお高度化を続ける電子機器。なかでも発展著しいのが、いわゆる情報機器です。モバイル機器はもはや当たり前の存在となり、ウェアラブルな電子機器が登場し、IoT(Internet of Things)でモノがインターネットにつながり始め、AI(人工知能)を活用した機器の研究も進んでいます。こうした進化の背景には、必ず半導体そのものの技術革新があります。その革新を支え、高度に進化してきたBT積層板も、現在、もう一つ高い次元を目指しているところ。半導体メーカーのトレンドを先取りする研究を進め、基板の性能向上という観点から、情報技術の未来を開拓していきます。
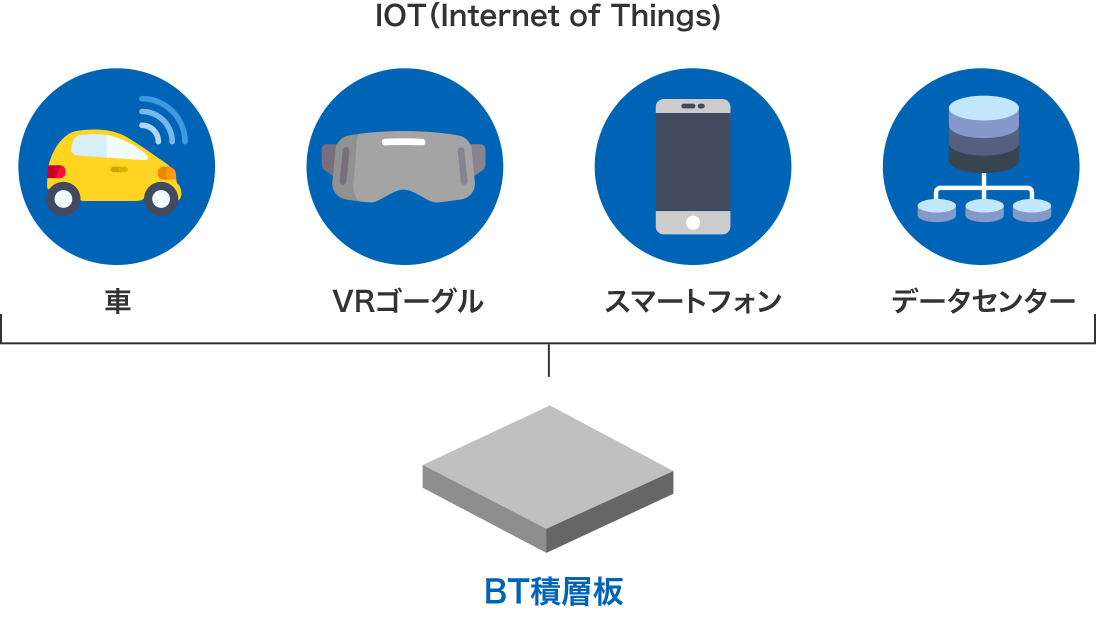