Nylon-MXD6/Nylon 6 Blended Film
Nylon-MXD6 has a dissolution index (SP value) close to Nylon 6 and Nylon 66 aliphatic polyamides, which undergo recrystallization. By mechanically blending Nylon-MXD6, Nylon 6 and Nylon 66 by means of co-extrusion and co-injection, Nylon-MXD6 can readily combine with these two types of Nylon, thereby allowing the manufacture of molded products such as films and sheets. Nylon-MXD6 has gas-barrier characteristics greater than any other commercially marketed nylon resins. By blending in Nylon-MXD6, you can efficiently increase gas-barrier characteristics of blended Nylon 6 and Nylon 66. The addition of Nylon 6 to Nylon-MXD6 is also beneficial to Nylon-MXD6; it prevents the whitening of Nylon-MXD6 when it absorbs moisture, while it also improves Nylon-MXD6's impact resistance.
Fig. 7 shows the relationship between the blending ratio and the oxygen transmission coefficient of the Nylon-MXD6/Nylon 6 blended film. Please contact MGC for further details about the selection and molding requirements of Nylon 6.
Fig.7 Relationship between the Nylon-MXD6/Nylon 6 Blending Ratio and the Oxygen Transmission Coefficient
Measuring Conditions : 23℃, 60%RH
Laminated film with an integral gas-barrier layer, achieved by blending Nylon-MXD6 and Nylon 6 retains excellent gas-barrier quality after it has been heated. Transparency is also retained. Table 8 shows the change in the oxygen transmission coefficient of laminated films after they are subjected to boiling. Fig. 8 shows the cumulative oxygen transmission coefficient of Nylon-MXD6/Nylon 6 blended film after it has been boiled.
Film Structure Thickness (μm) |
Haze (%) | Oxygen Transmission Coefficient (cc/m2·day·atm) |
|||||
---|---|---|---|---|---|---|---|
Before Boiling |
After Boiling |
Before Boiling |
Time after Boiling (hr) | ||||
1 | 10 | 24 | 72 | ||||
LLDPE/Tie/Blend/Tie/LLDPE 30/10/15/10/30 |
3.4 | 6.8 | 11 | 68 | 30 | 20 | 12 |
LLDPE/Tie/EVOH/Tie/LLDPE 30/10/15/10/30 |
5.1 | 59.2 | 11 | 400 | 165 | 46 | 12 |
Blend:Nylon-MXD6/Nylon-6=90/10 boil treatment 30min.,100℃.
Measurement condition: 23℃, inside:100%RH, outside:60%RH
Fig. 8 Cumulative Oxygen Transmission Coefficient of Nylon-MXD6/Nylon 6 Blended Films after Boiling
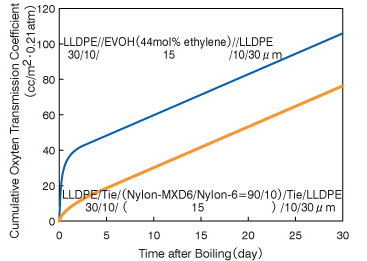
Boiling Conditions : 100℃, 30min
Measuring Conditions : 23℃, In 100℃RH, Out60%RH
Nylon-MXD6 laminated film locks in the original aroma, while blocking out foreign odors. Table 9 shows the aroma-retaining and odor-blocking properties of various gas-barrier films.
Barrier Material (Thickness:15µm) |
Evaluated Food | ||
---|---|---|---|
Soy Sauce | Vinegar | Worcester Sauce | |
Nylon-MXD6 (oriented) | ◎ (One Month) |
○ | ◎ (Three Months) |
Nylon-MXD6/Nylon 6Blend (oriented) | ◎ (One Month) |
○ | ○ |
Nylon 6 (oriented) | ○ | ▲ | ○ |
PVDC Coated Nylon 6 (oriented) | ◎ (One Month) |
○ | ○ |
PET (oriented) | ◎ (One Month) |
△ | △ |
PE | ▲ | ▲ | ▲ |
Barrier Materials (Thickness:15µm) | Evaluated Flavor | ||
d-limonene | Vanilla Essence | L-menthol | |
Nylon-MXD6 (oriented) | ◎ | ◎ | ◎ |
Nylon-MXD6/Nylon 6Blend (oriented) | ○ | △ | ◎ |
Nylon 6 (oriented) | ○ | ▲ | ◎ |
EVOH | ○ | △ | ◎ |
PVDC Coated Nylon 6 (oriented) | ◎ | ◎ | ◎ |
PET (oriented) | ○ | ◎ | ◎ |
PP (oriented) | ▲ | ▲ | ○ |
PE | ▲ | ▲ | ▲ |
Nylon-MXD6/Nylon 6 Blend (oriented) :Nylon-MXD6/Nylon 6=30/70
Condition:23℃, 50%RH (shaded from light)
Evaluation Method:Sensory Analysis
Odor-Blocking Period
◎ : no less than 2 weeks
○ : 1 or 2 weeks
△ : 3 days to one week
▲ : within 3 days
Inquiries Concerning Products
Green Energy & Chemicals Business Sector
High-performance Products Division
HP Material Department
TEL:+81-3-3283-4800 / FAX:+81-3-3214-0938